Regardless of the3D CAD package, Creo and SolidWorks being my tools of choice to cover majority of the industry I play in around Sydney and Australia, the dilemma is the same.
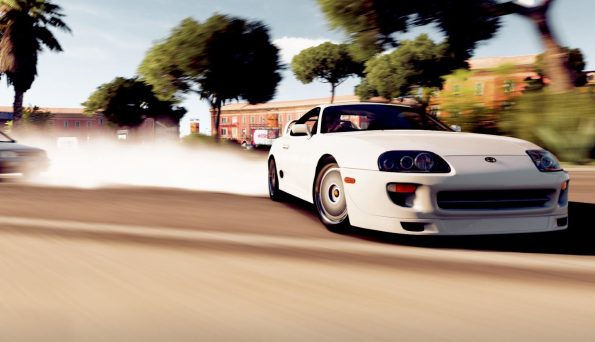
When we are starting to model at the concept phase of the development cycle, what is the best way forward….. Fast and Loose or Structured and Robust.
What do I mean by this, well it comes down to how we created our parts and assemblies, but more importantly how the parts and assemblies reference the components that they interact with in CAD and in their intended reality once they make it to the light of day?
Both have pros and cons.
So, what do I mean by fast and loose in terms of reference control?
This can also be termed bottom up.
This is the style of modelling where you build parts in CAD concurrently, selecting references within each part from the mating parts.
Bottom-Up Design can be a really quick way of blocking out multiple concepts of a product design in its early stages (depending on CAD experience).
It is a useful way of locking down a sense of size, shape, aesthetic form and part count within the assembly whilst we are still discovering how the product will evolve to meet all of its design brief objectives, both known and unknown.
These models are great for proof of concept. Potentially to create quick external renderings to engage stake holders who may or may not have a creative bent. It can be a fabulous way to get buy in from managers or financiers who by their makeup often can’t imagine what a concept could be but will make a decision based on something that they can conceptually see in front of them.
BUT…. The downside to fast and loose is robustness.
The risk of circular references is very high. A circular reference is when Part A reference Part B, and later through the development of Part B, it references back to Part A.
The result…when part A falls over, Part B falls over and then Part A falls over.
The circle or cycle continues until all references have been cleaned. This can take hours or in worst cases, days.
References disappear as the models evolve. Edges that are selected in an adjacent model in an assembly disappear as draft and rounds are added. This is especially prevalent for plastic injection moulded part design where drafts and rounds for tooling and moulding are necessity.
An alternative modelling style is Structured and Robust, also known as Top-Down design.
Top-Down Design is where the product size, shape and aesthetic form and all the part interactions are controlled by a top-level file called a skeleton (Creo) or Master Model (SolidWorks).
An example of Top-Down Design can be seen here. https://youtu.be/-TrCQ6NXgaA
So, which is best…Only you can decide, but choose wisely.
Comments