Valve gating is a specialised technique in injection Moulding that has gained prominence for its ability to improve efficiency, reduce waste, and enhance product quality.
As industries strive for more sustainable and cost-effective manufacturing solutions, valve gating has become a key component in achieving these goals.
This blog delves into the various benefits of valve gating and its applications across industries.
What is Valve Gating?
In the injection Moulding process, valve gating is a method of controlling the flow of molten plastic into the Mould cavity using a valve pin. Unlike conventional hot runner systems that rely on open gates, valve gating uses a mechanical or hydraulic mechanism to open and close the gate precisely.
This provides greater control over the injection process, resulting in improved efficiency and higher-quality parts due greater shot control.

Improved Surface Finish
One of the standout benefits of valve gating is the superior surface finish it enables. By precisely controlling the flow of material, valve gating minimizes blemishes, flow lines, and other defects that can occur at the gate location.
Key Advantages:
No Gate Marks: The pin retracts completely on injection and returns to match the cavity, leaving a smooth surface on the moulded part.
Gate flush with cavity surface. Enhanced Aesthetics: Ideal for parts where appearance is critical, such as consumer goods and automotive components.
Reduced Post-Processing: Eliminates the need for additional finishing steps like sanding or polishing.
Elimination of Stringing and Drooling
Stringing and drooling, common challenges in traditional hot runner systems, occur when molten plastic leaks or forms strings at the gate. Valve gating solves this problem by mechanically sealing the gate during non-injection phases.
Benefits Include:
Cleaner Moulds: Reduces contamination of the Mould cavity.
Improved Part Consistency: Ensures that each part is uniform, without unwanted material build up.
Enhanced Productivity: Minimizes downtime associated with cleaning and maintenance.
Control of material in the Barrel: With the valve gate shutting off material in the nozzle from the cavity, this material remains molten and active ready for the next shot.
Reduced Cycle Times
Cycle time is a critical metric in injection Moulding, directly affecting productivity and profitability. Valve gating contributes to faster cycle times by enabling:
Optimised Flow Control: Ensures a smooth and controlled filling process, reducing cooling time.
Faster Mould Closure: The precise gating mechanism allows for quicker gate sealing.
Minimized Overpacking: Prevents excess material from entering the Mould, reducing the cooling phase.
Shorter cycle times mean higher throughput and cheaper parts, making valve gating an invaluable tool for high-volume production.
Material Savings
By reducing overpacking and ensuring precise material usage, valve gating helps manufacturers save on raw materials. This is especially beneficial for expensive engineering-grade plastics.
How It Saves Material:
Eliminates Sprues and Runners: Material wastage from traditional gating systems is significantly reduced.

Optimized Fill Volume: Delivers only the necessary amount of plastic to each cavity.
Recyclable Excess: The minimal excess material can be easily reprocessed and reused.
Material savings not only cut costs but also contribute to more sustainable manufacturing practices.
Enhanced Dimensional Accuracy
Dimensional accuracy is critical in industries such as aerospace, automotive, and medical devices. Valve gating ensures that each part is produced with consistent dimensions by controlling the flow and pressure of molten plastic.
Advantages in Accuracy:
Uniform Filling: Prevents variations in part thickness or weight.
Improved Repeatability: Ensures that every part meets tight tolerances.
Reduced Warpage: Controlled injection reduces internal stresses, minimizing deformation.
Greater Design Flexibility
Valve gating expands the possibilities for part design by enabling:
Multiple Gate Locations: Allows for complex and large parts to be filled uniformly. This process is used for parts with long flow paths like car bumper bars. In this application, where weld lines are weak points, sequential valve gates keep the melt front active, molten and controlled with no weld lines along the length of the part.


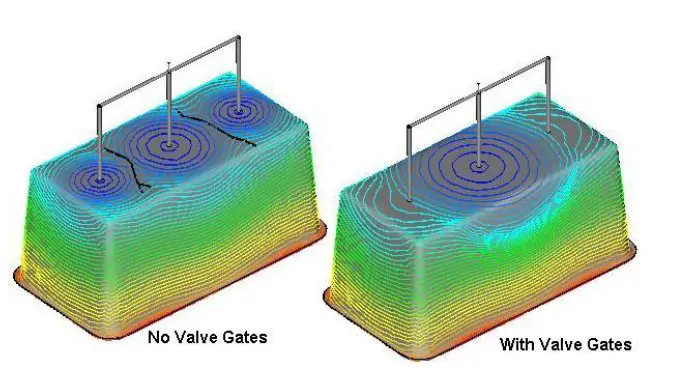
Smaller Gates: Precision gating accommodates intricate designs without compromising strength.
Balanced Multi-Cavity Moulds: Ensures consistent quality across all cavities in multi-cavity Moulds.
This flexibility is especially valuable in industries requiring innovative designs, such as electronics and consumer goods.
Improved Efficiency in Multi-Cavity Moulds
For multi-cavity Moulds, uniform filling of all cavities is crucial to avoid imbalances and defects. Valve gating ensures:
Consistent Flow Distribution: Prevents overfilling or underfilling in specific cavities.
Reduced Scrap Rates: Produces uniform parts across all cavities, minimizing rejects.
Higher Yield Rates: Maximizes the number of usable parts per cycle.
These advantages make valve gating ideal for large-scale production runs.
Reduced Maintenance Costs
The precise control offered by valve gating reduces wear and tear on the Mould and associated components. By eliminating issues like stringing and overpacking, manufacturers can:
Extend Mould Life: Minimize damage to Mould surfaces.
Lower Repair Costs: Avoid frequent repairs due to gate-related issues.
Increase Uptime: Reduce downtime caused by maintenance interruptions.
Compatibility with Advanced Materials
As industries shift towards lightweight and high-performance materials, valve gating’s precision becomes increasingly important. It is particularly beneficial when working with:
Filled Plastics: Ensures uniform distribution of fillers like glass or carbon fibres.
High-Temperature Polymers: Prevents degradation by maintaining controlled flow and pressure.
Bioplastics: Reduces material wastage, supporting eco-friendly manufacturing.
Sustainability and Environmental Benefits
Valve gating aligns with the growing demand for sustainable manufacturing by:
Reducing Waste: Minimizes material wastage and scrap rates.
Energy Efficiency: Shorter cycle times and reduced material usage lower energy consumption.
Supporting Recycling: Clean gate closures facilitate easier recycling of excess material.
These benefits contribute to a greener manufacturing process, meeting regulatory requirements and consumer expectations.
Applications of Valve Gating
Valve gating is widely used across various industries, including:
Automotive: Producing lightweight and aesthetically appealing components.
Medical: Manufacturing precision devices and implants.
Consumer Goods: Creating durable and visually appealing products.
Electronics: Enabling intricate and functional designs for housings and components.
Valve Gating's versatility makes it a go-to solution for high-quality injection Moulding projects.
Valve gating offers a host of benefits, from improved surface finishes and dimensional accuracy to reduced cycle times and material savings. By enhancing efficiency and supporting sustainable practices, valve gating has become a critical tool in modern injection Moulding.
Whether for high-volume production or intricate designs, valve gating provides the precision and reliability needed to meet the demands of today’s industries.
As manufacturers continue to prioritize efficiency and sustainability, valve gating’s role in injection Moulding will only grow. By investing in this technology, companies can not only enhance their operations but also stay ahead in an increasingly competitive market.
-----
équipe design & consulting is a Product Design Consultant in Sydney.
With 20 years’ experience in design and manufacture of Medical grade moulded parts and product, including 5 years at the coal face as Operations Manager at a world class medical grade moulding facility; we are specialist in Design for Manufacture (DFM).
Please reach out if you feel you need assistance with your part design for plastic injection moulding.
We offer Design Coaching and Guidance to Full-Service Design Consulting.
#Designforplasticinjectionmoulding #DesignForManufacturing #DesignThinking #DesignforManufacture #DesignConsulting #DesignCoaching #equipedesign #DesignforAssembly #IndustrialDesign #CREODesign
References: ChatGPT, Google Images, VEM Tooling
Коментарі