Following on from a previous 2-part blog - 10 Impacts of Non-Uniform Wall Sections in Plastic Injection Moulded Parts (see here) being only a brief over view of a complex topic, it seemed the next appropriate step was a deeper dive into the outlined Negative Impacts in more detail to highlight how a seemingly minor design detail can have a significant impact on the productivity, efficiency and therefore competitive advantage of an injection moulded part and its success out in the market.
First a little revision of Impact no.6 from Part 1 of the blog.
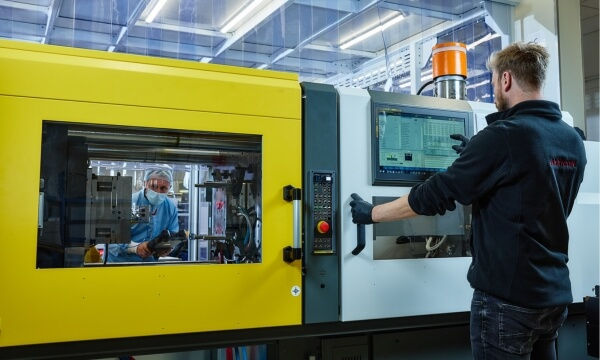
“6. Increased Cycle Time and Costs
Parts with non-uniform wall sections typically require longer cooling times, as the thicker sections need more time to solidify. The part cycle time is driven by the thickest portions of the part, regardless if the majority of the part is thinner and uniform, in order to control part quality in the thick portion.
Extended cooling periods increase the overall cycle time. The moulder must hold the part in the controlled environment of the tool for longer periods to ensure that warping is controlled in situ and the part is stable (solidified) enough to be ejected. Effectively reducing the production efficiency of the injection moulding process.
A general rule is double the wall section, quadruple the cycle time.”
Cycle time is the major contributor of total part cost. It is a fairly simple formulae - the hourly machine rate divided by how many shots/cycles can be produced in an hour (possibly increased by cavitation). An increase in cycle time reduces the hourly output and directly increases the part cost.”
To analyse the impact in a real-world scenario faced by many designers...
Let’s assume a designer has a part design that is failing to meet its structural requirement during FEA analysis. A less experienced designer may merely thicken the wall section in the area of failure to achieve a passing result. The impact though is that the cost increase may be significant, but not how you may think.
So, what are the numbers behind this impact of the thicker wall section.
It is a common misconception that for a thicker wall sections, it is the extra material consumption has a greater impact on part cost.
To put this in dollar terms, consider the following scenario; if the part above is 50 grams and is moulded in a $20/kg material, assuming a hot tip injection with no runner waist, the material component cost is $1 per part.
Let’s assume the design change increased the part weight by 5% in the required area.
The resultant part cost increase is an additional 10 cents. So, a new material cost of the part is $1.10.
In comparison let’s assume the change doubled the wall section in this area of the part, say 2mm to 4mm. The cycle time would increase from 20 seconds to 80 seconds to ensure part stability on ejection.
The cycle time impact has a direct correlation on tool hourly productivity.
There are 3600 seconds in an hour. A 20 second cycle produces 180 shots from a single cavity tool. An increase in cycle time to 80 seconds now only produces 45 shots per hour,
Moulding machines are generally charged out at an hourly rate dependant on size, footprint, energy consumption etc. Let’s assume $50/hour.
The machine rate portion of each individual part cost for the above cycle time increase climbs from $0.28 per part to $1.11 per part.
For comparison the material component increased by 10 cents, the cycle time component increased by 83 cents.
The part cost for more material consumption PLUS a longer cycle time has increased from $1.28 to $2.21.
Now magnify that by mass production annual volumes of 10,000, 100,000 or millions.
As a side impact to compound the issue, the variable wall section of the part design may necessitate more intricate mould designs with better cooling and additional machining, leading to higher tooling costs.
Whilst this is a fictional scenario, the reality of moulding being influenced by a myriad of variable and cumulative factors, they collectively highlight the direct impact of a part design that is not optimised to make the very best efficiencies and productivity of the Plastic Injection Moulding Process.
As designers we wish to create parts and product that meet the customers requirements for fit form and function, but also will be successful out in the real world.
In the scenario above, rather than merely thickening the wall section an optimised part design would incorporate different design techniques to achieve the functional requirement for greater strength without adding cost. Design features like ribbing or gussets or the use of changes in wall geometry in the required area can achieve the same functional outcome, but now optimised for high volume plastic injection moulding.
To give our designs the best possible chance of success special care is needed for every design made throughout the development process.
Uniform wall sections in parts designed for plastic injection moulding is but one input into the design process, but one that needs due respect.
---
équipe design & consulting , with 20 years experience in design and manufacture of Medical grade moulded parts and product, including 5 years at the coal face as Operations Manager at a world class medical grade moulding facility; we are specialist in Design for Manufacture (DFM).
Please reach out if you feel you need assistance with your part design for plastic injection moulding, from Design Coaching and Guidance to Full Service Design Consulting.
Comments