Even with the growth of the new frontier of additive manufacturing in recent years, Plastic injection moulding is still the front runner for economical high-volume production of many Industrial, Consumer and Medical products. This is largely due to its production efficiencies, reduced cycle times, and achievable part accuracy and quality.
However, achieving optimal results requires careful part design consideration and quality tooling. Unlike the freedoms of properties and processes of additive manufacturing Plastic Injection Moulding comes with certain rules or guidelines that must be respected to ensure parts meets the required specification. Knowing how far the designer can push the boundaries for each unique part comes with experience.
For part design, one area in particular that directly effects production efficiencies and in market competitiveness of a part or product, achievable part accuracy and quality is the wall thickness of the moulded parts. Non-uniform wall sections, where the thickness of the part varies throughout its structure across the part, can lead to several significant downsides.
This 2-part blog explores 10 key negative impacts associated with non-uniform wall sections in plastic injection moulded parts.
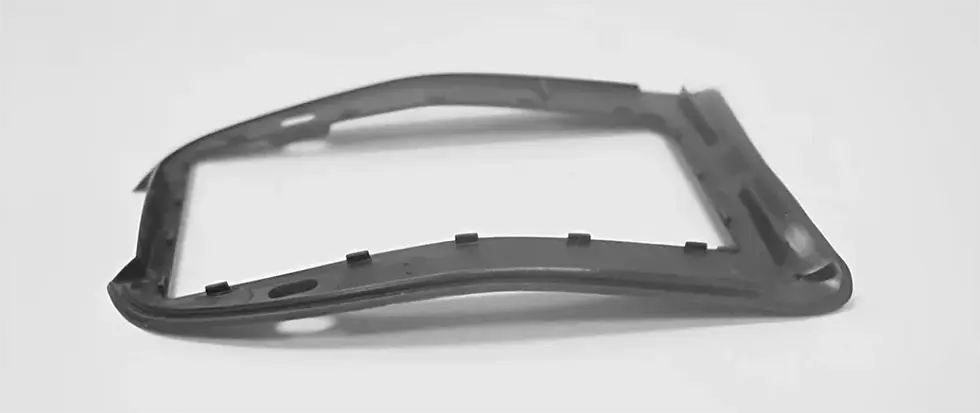
1. Warpage and Distortion
One of the primary problems caused by non-uniform wall sections is warpage and distortion. During the cooling phase of the injection moulding process, different sections of the part cool and solidify at different rates due to their varying thicknesses. Thicker sections cool more slowly than thinner ones, creating internal stresses within the part. These stresses can lead to warping, where the part bends or twists out of its intended shape. Warpage not only affects the aesthetic quality of the part but can also impair its functional performance, potentially leading to assembly issues or failure in service.
2. Difficulties in Achieving Accurate Dimensional Tolerances
Maintaining tight dimensional tolerances is crucial for the fit and function of plastic parts, especially in high-precision applications. Non-uniform wall sections can complicate the moulding process, making it more challenging to achieve the desired dimensional accuracy. The differential cooling rates and resultant warpage can lead to deviations from the intended dimensions, requiring additional post-moulding operations such as machining or trimming. At best these additional steps not only add to the production costs but can also introduce further variability and potential defects. At worst the parts may be scrapped altogether, increasing the overall cost to the manufacturer and in the end, the customer.
In medical grade moulding with Process Capability (CPK) requirements, a process range within a tolerance part dimensional accuracy, repeatability and reliability become even more crucial.
3. Challenges in Structural Integrity and Performance
For parts that require high structural integrity and performance, non-uniform wall sections can be particularly detrimental. The internal stresses, warpage, and potential voids can all contribute to a reduction in the part’s overall strength and durability. In critical applications such as automotive components, medical devices, or aerospace parts, these issues can lead to significant safety concerns and reliability problems. Ensuring uniform wall thickness is essential for maintaining the required performance standards and ensuring the safety and reliability of the final product.
4. Sink Marks and Voids
Non-uniform wall sections are prone to sink marks and voids. Sink marks are depressions or indentations that appear on the surface of the part, typically above thicker sections where the material has contracted more during cooling. These marks are not just visually unappealing but can also indicate underlying structural weaknesses. Voids are empty spaces within the part caused by insufficient material flow or air trap seen as bubbles when a apart is cross sectioned. As well as being visually unsightly, possibly failing aesthetic criteria of a specification, sink marks and voids compromise the mechanical integrity of the part, making it less durable and more susceptible to failure under load.
In certain markets like the medical and consumer industries where a high investment in and therefore a high emphasis placed on the aesthetic quality of a part, a seemingly structurally viable part may be scrapped as it fails a visual criterion.
5. Poor Material Flow
Uniform wall thickness is crucial for ensuring smooth and consistent material flow during the injection moulding process. Non-uniform sections can lead to poor flow characteristics, resulting in incomplete filling of the mould or the formation of weld lines. As material flows into a cavity it forms a skin, a surface layer at the flow front and where it contacts the cavity wall that is cooler than the material behind it I the middle of the flow. Weld lines occur where two flow of these cooler fronts meet and attempt to re-join. At this point of welding the two cooler fronts or skins cannot re-join as effectively as the hotter material behind them. The result is a weld line, creating a weak spot in the part.
Poor material flow can also cause air entrapment, leading to voids and further weakening the part. A good toolmaker may be able to minimise this occurrence along a part line or insert with venting, but it is better to resolve the issue in part design rather than Band-Aids in tooling.
Ensuring a consistent wall thickness helps in maintaining a balanced and controlled flow, reducing the risk of defects.
Stay tuned for part 2. for the next 5 Impacts of Non-Uniform Wall Sections in Plastic Injection Moulded Parts.
---
équipe design & consulting , with 20 years experience in design and manufacture of Medical grade moulded parts and product, including 5 years at the coal face as Operations Manager at a world class medical grade moulding facility; we are specialist in Design for Manufacture (DFM).
Please reach out if you feel you need assistance with your part design for plastic injection moulding, from Design Coaching and Guidance to Full Service Design Consulting.
Comments